Which type of grinding wheel is best for hard materials?
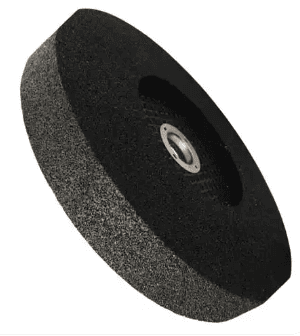
own aluminum oxide has high hardness and toughness, making it suitable for grinding metals with high tensile strength, such as carbon steel, alloy steel, malleable cast iron, and hard bronze. This abrasive offers excellent grinding performance, wide adaptability, and is commonly used for heavy stock removal in rough grinding. It is cost-effective and widely applicable.
Which Grinding Wheel is Suitable for Cast Iron?
The most commonly used abrasives are brown aluminum oxide (A) and white aluminum oxide (WA), followed by black silicon carbide (C) and green silicon carbide (GC). Other frequently used abrasives include chromium oxide (PA), monocrystalline aluminum oxide (SA), microcrystalline aluminum oxide (MA), and zirconia alumina (ZA).
- Brown Aluminum Oxide Wheel (A):
High hardness and toughness, ideal for grinding high-tensile metals like carbon steel, alloy steel, malleable cast iron, and hard bronze. Offers good grinding performance, wide adaptability, and is often used for heavy stock removal in rough grinding. Cost-effective and widely used. - White Aluminum Oxide Wheel (WA):
Slightly harder than brown aluminum oxide but less tough. The abrasive grains fracture more easily during grinding, reducing heat generation. Suitable for precision grinding of hardened steel, high-carbon steel, high-speed steel, and thin-walled parts. More expensive than brown aluminum oxide.
Classification of Grinding Wheels
Grinding wheels come in various types:
- By abrasive material: Conventional abrasive wheels (aluminum oxide, silicon carbide, etc.) and superabrasive wheels (diamond, cubic boron nitride, etc.).
- By shape: Flat wheels, tapered wheels, cylindrical wheels, cup wheels, dish wheels, etc.
- By bond type: Vitrified (ceramic) wheels, resin wheels, rubber wheels, metal-bonded wheels, etc.
Key parameters of grinding wheels:
- Abrasive type
- Grit size
- Hardness
- Bond type
- Shape and dimensions
Since grinding wheels operate at high speeds, they must undergo rotation tests (to ensure they won’t break at working speeds) and static balance tests (to prevent machine vibration) before use.
What Materials are Diamond Grinding Wheels Suitable For?
Diamond grinding wheels are ideal for machining hard, brittle non-metallic materials and cemented carbides due to their high hardness, compressive strength, and wear resistance. They are widely used in processing:
- Glass
- Ceramics
- Magnetic materials
- Integrated circuits
- Gemstones
- Stone
- Tiles
- Concrete
- Refractory materials
Compared to conventional abrasives (boron carbide, silicon carbide, aluminum oxide), diamond wheels offer:
- Sharper cutting edges
- Longer service life
- Higher productivity
- Better surface finish
However, they are more expensive and are mainly used for precision grinding of hard, brittle, and difficult-to-machine materials like cemented carbide, ceramics, and semiconductors.
Types of Diamond Grinding Wheel Bonds
Based on bonding strength and wear resistance:
- Resin-bonded wheels
- Vitrified (ceramic) wheels
- Metal-bonded (bronze) wheels
- Electroplated metal wheels
Commonly used types:
- Vitrified-bonded diamond wheels:
Used for PCD (polycrystalline diamond) inserts, PCBN (polycrystalline cubic boron nitride) inserts, carbide/ceramic tools.
Performance is between resin and metal-bonded wheels—more durable than resin wheels but sharper than bronze wheels. - Resin-bonded diamond wheels:
Mainly used for grinding ultra-hard alloys, non-metallic materials, cutting hard and brittle materials (e.g., carbide, ceramics, agate, optical glass, semiconductors, wear-resistant cast iron, stone).
Selection Criteria for Diamond Grinding Wheels
Key factors:
- Abrasive type: Synthetic diamond (JR), selected based on crystal shape and grain strength.
- Grit size: Determines surface finish, grinding efficiency, and diamond consumption.
- Concentration:
- High concentration → Better shape retention
- Low concentration → Lower diamond consumption
- Shape & dimensions: Must match the grinder and workpiece requirements.
For resin-bonded diamond wheels, hardness (usually S/Y1 grade or higher) must also be considered.
Challenges with Vitrified Diamond Wheels
Vitrified bonds require extremely high sintering temperatures, which can damage diamond abrasives. Progress in low-temperature vitrified bonds has been slow. Current alternatives include:
- Modified resin wheels: Adding copper powder to improve heat resistance and durability.
- Modified bronze wheels: Adding brittle fillers to enhance self-sharpening.
These alternatives have partially replaced vitrified diamond wheels in certain applications.