Can a core drill cut through rebar?
yes, a core drill can cut through rebar.
1. Can Hollow Drills Penetrate Rebar?
Hollow drills are tools capable of drilling through concrete and rebar, but they cannot penetrate rebar in all cases. Since rebar is a relatively hard material, sufficient pressure must be applied to the drill bit to penetrate the rebar and continue drilling downward. Therefore, when using a hollow drill, it is essential to select the appropriate drill bit, apply the correct rotational speed, and exert suitable pressure to successfully penetrate the rebar.
2. Precautions When Using Hollow Drills
- Selecting the Right Drill Bit
Different materials require different drill bits. When using a hollow drill, the bit must be chosen based on the material being drilled. Additionally, drill bits of varying diameters correspond to different hole sizes, so the appropriate bit must be selected according to the required aperture. - Applying Proper Pressure
Applying the right amount of pressure helps the drill bit penetrate rebar and concrete more effectively while controlling drilling progress. However, excessive pressure may damage the bit or shorten its lifespan. Therefore, moderate pressure should be applied to avoid equipment damage. - Controlling Rotational Speed
An appropriate rotational speed improves drilling efficiency, but speeds that are too high or too low can negatively affect performance. Thus, the speed should be adjusted based on the required hole size and the material being drilled.
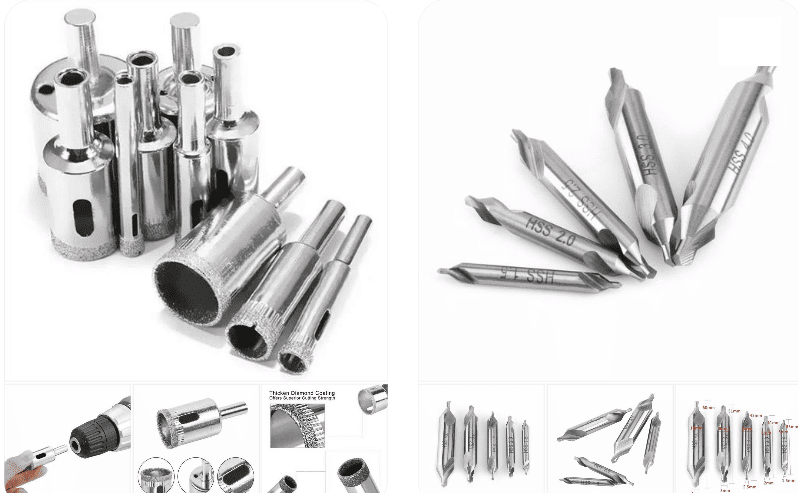
3. Key Considerations When Drilling Rebar with Hollow Drills
When using a hollow drill to penetrate rebar, it is crucial to choose the right drill bit, apply proper pressure, and control the rotational speed to ensure successful drilling. Additionally, the following points should be noted:
- Replace severely worn drill bits promptly.
- Maintain equipment stability and drilling direction during the process.
- Clean debris from the hole walls after drilling.
In summary, when using hollow drills, appropriate methods and precautions must be followed to ensure successful drilling and protect the equipment. Avoid reckless operation during use.
Innovation and Efficiency Analysis of Hollow Drills in Steel Structure Manufacturing
The latest hollow drill technology revolutionizes steel structure drilling processes, improving efficiency by 3-5 times and speed by 8-10 times. It meets the demands of large-diameter and deep-hole machining while optimizing heat management during cutting, enhancing both safety and cost-effectiveness.
Current State and Challenges in the Steel Structure Industry
In recent years, steel structures have gained widespread application across various fields—including large-span structures, industrial plants, thermal and nuclear power facilities, multi-story and high-rise buildings, towering structures, and pressure vessels—due to their excellent workability, weldability, high strength, lightweight nature, and uniform material properties. With sustained economic growth and rapid technological advancements, the use of steel structures continues to expand, leading to the emergence of numerous manufacturing and installation enterprises and driving the industry’s vigorous development.
In steel structure manufacturing, hole-making is a critical process, especially with the introduction of high-strength bolts, which impose higher demands on both the quantity and precision of holes. For instance, a production line with a monthly output of about 800 tons of steel structures requires the drilling of over 2,000 high-strength bolt holes daily—a task that traditional drilling methods struggle to meet efficiently.
- CNC cutting machines produce holes with rough walls, flame-cut marks, and oxidation layers, failing to meet precision requirements.
- Standard twist drills used on radial drilling machines ensure accuracy but require clamping, limiting efficiency.
- CNC drilling machines are restricted to steel plates and angle steels, making them unsuitable for large components.
Thus, there is an urgent need for innovative tools to overcome the limitations of conventional methods.
Structure and Performance of the New Hollow Drill
The new hollow drill (also called a core drill) features a unique multi-blade annular cutting design. With a drilling diameter range of 12–150 mm, it is ideal for steel component drilling in industries such as steel structure engineering, rail transit, bridges, shipbuilding, machinery manufacturing, and aerospace.
Compared to traditional two-flute twist drills, the new hollow drill offers 3–5 times higher efficiency and 8–10 times faster drilling speeds.
Design Features of the Drill Bit
When paired with multi-blade plate drills and magnetic drill presses, the new hollow drill effortlessly handles multi-directional drilling on large steel components, significantly reducing construction time. Its design enhances precision while accommodating various steel component specifications. Additionally, hollow drills come in different cutting depths, including 25 mm, 35 mm, 50 mm, 75 mm, and 100 mm.
Cutting Edge Design
The innovative hollow drill adopts a three-combination-blade structure with uneven tooth spacing and specially designed carbide cutting edges, greatly improving cutting efficiency. The geometric parameters of the cutting edges ensure stability and precision while reducing the risk of edge chipping. Each blade bears only about one-third of the workload, ensuring long-term durability.
Efficiency Advantages
Thanks to its unique design, the hollow drill expands the cutting range, enabling efficient machining of large-diameter and deep holes with minimal power. Its flexible sizing reduces costs, enhances speed and effectiveness, and outperforms traditional twist drills in penetrating hard materials.
Heat Management and Chip Disposal
The new hollow drill utilizes internal coolant spraying for effective temperature control, significantly improving safety and extending the tool’s lifespan. Additionally, it produces cylindrical steel chips with high recycling value, unlike the long, spiral chips from standard twist drills, further enhancing safety and cost-efficiency.
Conclusion
The advent of the new hollow drill represents a technological breakthrough in steel structure manufacturing. As industry standards continue to rise, the hollow drill, with its distinct advantages, is poised to become the preferred tool for drilling operations in steel structure production.
Friendly Links: small grinder machine, Level 3 EV Charger, Filling and Capping Machine, irregular plastic bag irregular shaped Package.