What size hole for core drilling?
The aperture range of core drills varies depending on their application:
Industrial Sector
- Standard Drilling: Common apertures range from 12mm to 150mm, suitable for steel structure engineering, rail transit, shipbuilding, and other fields, capable of drilling holes up to 150mm in diameter.
- High-Efficiency Drilling: Some models support larger apertures, such as drilling a 40mm diameter hole in 25–40 seconds (for a 30mm-thick steel plate).
Medical Equipment Sector
- Medical Applications: Used in orthopedic or neurosurgical procedures, though specific aperture sizes are not explicitly mentioned in search results.
For more precise parameters, it is recommended to consider the specific application scenario (e.g., material thickness, processing requirements) for further confirmation.
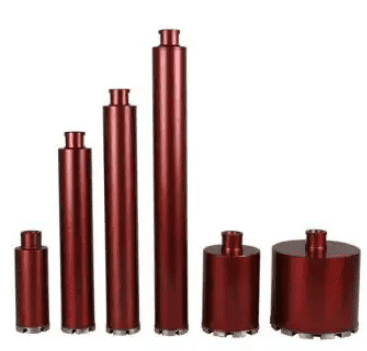
What Is the Diameter of a Core Drill Bit?
The diameter of core drill bits typically ranges from 12 millimeters (mm) to 160 millimeters (mm), with different specifications suited for various drilling needs and applications. These diameter figures are based on industry standards and professional manufacturers, ensuring accuracy and reliability.
I. Overview of Core Drill Bit Diameters
Core drill bits, as high-efficiency drilling tools, come in diverse diameter specifications to meet the needs of different industries and projects. Generally, the diameter of core drill bits can vary from 12mm to 160mm. This wide range allows core drill bits to be flexibly applied in various drilling scenarios, whether for precision machining or large-aperture excavation.
II. Applications of Different Diameter Specifications
- Small Diameter (12–35mm): Suitable for precision machining and small-aperture drilling, commonly used in electronics, telecommunications, medical devices, and other fields where drilling accuracy and quality are critical.
- Medium Diameter (50–100mm): Widely used in infrastructure construction, such as buildings, bridges, and rail transit. These sizes ensure drilling efficiency while maintaining hole accuracy and wall smoothness.
- Large Diameter (120–160mm): Primarily used for excavation in large-scale engineering projects, such as hydraulic engineering and mining exploration. Large-diameter core drill bits can quickly remove material, improving efficiency and reducing costs.
III. Key Considerations When Selecting Diameter
When choosing a core drill bit diameter, consider the following factors:
- Project Requirements: Select the appropriate diameter based on specific engineering needs and drilling purposes.
- Material Properties: Different materials affect bit wear, so choose a diameter suitable for the material’s hardness and toughness.
- Equipment Compatibility: Ensure the selected diameter matches the drilling equipment to maximize performance.
In summary, core drill bits cover a broad diameter range, from 12mm to 160mm. Selection should be based on specific requirements and conditions to ensure drilling efficiency and quality.
Detailed Specifications of Core Drills
I. What Is a Core Drill?
A core drill is a hollow drill bit with an internal cavity, used for drilling deep holes, large holes, or multiple holes. It is primarily applied in metal, wood, plastic, and other materials for hole-making processes.
II. Core Drill Specifications
- Diameter
- Core drills typically range from 10mm to 400mm in diameter. Different diameters are suited for different hole sizes; larger diameters correspond to larger holes.
- Length
- The length varies with diameter, generally between 60mm and 2000mm. Select the appropriate length based on the required hole depth.
- Number of Teeth
- Core drills usually have 4–8 teeth. More teeth improve machining quality, but material hardness and drilling depth must also be considered.
- Pipe Diameter
- The pipe diameter typically ranges from 2mm to 20mm. Choose based on the desired hole size.
- Cutting Depth
- The cutting depth varies by diameter, generally between 50mm and 1000mm. Select based on the required hole depth.
III. Considerations When Choosing a Core Drill
- Select the appropriate model and specifications based on the material (e.g., brass, cast iron, aluminum alloy, stainless steel).
- Choose the right diameter, length, and cutting depth for the desired hole size and depth.
- Pay attention to cooling, lubrication, and cutting speed to ensure machining quality.
- Prioritize operator safety to avoid injuries.
The above details the specifications of core drills, helping you select the right tool for precise and efficient hole drilling.
Friend Links: you may also interest in, click if you want: Dry Fruit Powder Grinder Machine customization, Mode 2 Charging Box for Sale, Piston filling machine customization, plastic film roll package customization.